Comprehensive Guide to Industrial Electronic Equipment
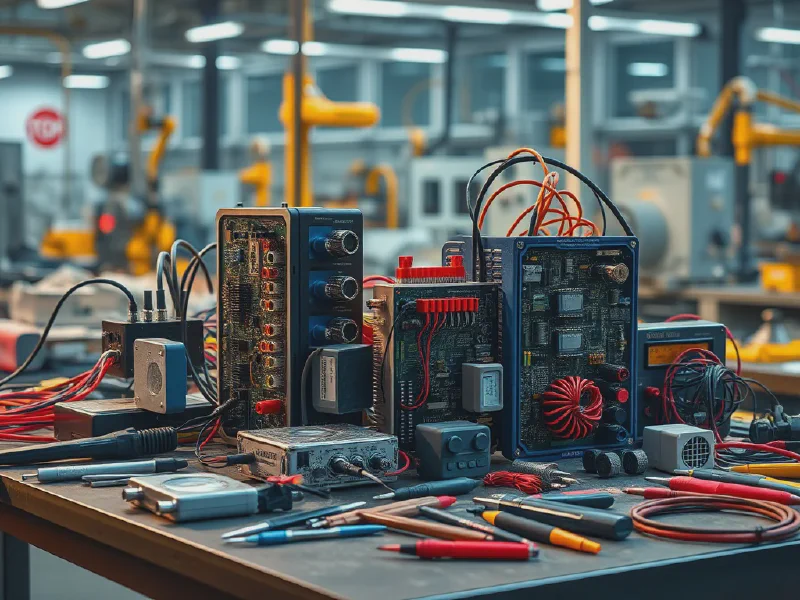
Understanding Industrial Electronic Equipment
Industrial Electronic Equipment comprises a range of electronic devices and components used in industrial applications to monitor, control, and automate various processes. This equipment plays a critical role in increasing efficiency, productivity, and safety within industrial environments. From manufacturing plants to power generation facilities, the proper functioning of industrial electronic equipment is essential for streamlined operations and minimal downtime.
Industrial Electronic Equipment serves as the backbone of modern industrial operations, encompassing programmable logic controllers (PLC), human-machine interfaces (HMI), sensors, drives, industrial controllers, and more. With the continuous advancement of technology, these devices are becoming increasingly sophisticated, contributing to smarter and more efficient industrial processes. As industries evolve, the reliance on industrial electronic equipment is becoming more pronounced, leading to better resource utilization and improved operational performance.
The importance of Industrial Electronic Equipment cannot be overstated, as these tools facilitate real-time data gathering, monitoring, and analysis, enabling organizations to make informed decisions quickly. With the integration of advanced technologies such as the Internet of Things (IoT) and artificial intelligence (AI), industrial electronic equipment is transforming how industries operate. This article delves into the types, applications, maintenance, future trends, and how to choose the right suppliers for industrial electronic equipment.
In a competitive industrial landscape, organizations must leverage Industrial Electronic Equipment to streamline processes and enhance productivity. Understanding the various components, their functionalities, and their real-world applications is crucial for any business looking to invest in industrial automation and efficiency. This understanding not only aids in optimizing operations but also ensures maximum reliability and longevity of the equipment in use.
in the age of tech, a dust resistant keyboard is essential for maintaining optimal performance and longevity in your devices.
The landscape of Industrial Electronic Equipment is vast and multifaceted, offering numerous solutions tailored to specific industrial needs. As technology continues to evolve, staying abreast of the latest advancements is essential for organizations aiming to maintain a competitive edge in their respective markets.
investing in a plug in power meter can significantly lower your energy costs by providing real-time data on consumption.
Types of Industrial Electronic Equipment
One of the most critical components of Industrial Electronic Equipment is the Programmable Logic Controller (PLC). These devices are used to automate industrial processes by receiving input signals, processing them according to pre-programmed instructions, and providing output signals to control machinery and equipment. PLCs are known for their rugged design and reliability, making them suitable for harsh industrial environments.
Human Machine Interfaces (HMI) serve as the communication bridge between operators and machinery. These interfaces allow users to monitor and control various industrial processes through visual representations displayed on screens. HMIs provide essential information in real-time, enabling operators to make quick decisions and adjustments to optimize production efficiency.
for anyone seeking efficiency in energy monitoring, the best plug in power meter australia offers unbeatable accuracy and user-friendly features.
Sensors and transducers are critical for data acquisition and monitoring in industrial applications. These devices convert physical quantities such as temperature, pressure, and motion into electrical signals that can be processed and analyzed. With accurate and reliable sensors in place, businesses can improve process control and ensure quality standards are met.
Drives and motors are responsible for converting electrical energy into mechanical motion. This category includes variable frequency drives (VFD) and servo motors, which allow for precise control of speed, torque, and position in various industrial applications. The efficiency of drives and motors directly impacts the overall performance and energy consumption of industrial equipment.
Industrial controllers are integrated systems that manage various industrial processes, incorporating multiple features such as automation control, data acquisition, and communication with other devices. These controllers enable centralized management of industrial operations, thereby improving coordination, efficiency, and responsiveness to changing production demands.
Applications of Industrial Electronic Equipment
Manufacturing Automation is one of the primary applications of Industrial Electronic Equipment. The integration of PLCs, HMIs, and sensors allows for the automation of manufacturing processes, significantly enhancing productivity, reducing labor costs, and minimizing human error. This automation is essential for meeting increasing production demands and maintaining competitive advantage in the industry.
Process Control systems utilize Industrial Electronic Equipment to monitor and control physical processes in industries such as chemical manufacturing, food processing, and oil refining. These systems rely on precise measurements from sensors and feedback mechanisms to maintain optimal operating conditions and ensure product quality. Effective process control also contributes to safety and regulatory compliance.
Robotics and Automation integrate Industrial Electronic Equipment to create sophisticated automated systems capable of performing complex tasks. These systems can work in environments that are dangerous for humans, such as in heavy manufacturing or hazardous materials handling. The use of industrial robots equipped with advanced sensors and control systems can significantly improve efficiency and precision in operations.
Power Generation facilities utilize Industrial Electronic Equipment for both the generation and distribution of electrical power. Equipment such as turbine controls, switchgear, and monitoring systems ensure that power generation processes run smoothly and efficiently. The integration of advanced sensors and controllers in power plants enhances reliability and performance.
Telecommunications heavily depend on Industrial Electronic Equipment for managing and maintaining communication infrastructure. From controlling network operations to ensuring the reliability of service, these electronic devices facilitate the smooth functioning of telecommunication systems, which are vital for connectivity in today’s digital world.
Maintenance and Reliability of Industrial Electronic Equipment
Preventive maintenance strategies are essential for prolonging the lifespan of Industrial Electronic Equipment and reducing the risk of unexpected failures. Regular inspections, scheduled maintenance, and timely upgrades help identify potential issues before they escalate, ultimately minimizing downtime and ensuring operational continuity.
Troubleshooting techniques play a vital role in maintaining the reliability of Industrial Electronic Equipment. Skilled technicians utilize various diagnostic tools and methodologies to identify and address issues in electronic systems. Efficient troubleshooting practices not only restore functionality but also enhance the overall reliability of the equipment.
Lifecycle management of Industrial Electronic Equipment involves overseeing the entire lifespan of the equipment, from initial procurement to installation, operation, and eventual retirement. An effective lifecycle management strategy ensures that equipment is properly maintained, upgraded, or replaced in a timely manner, thereby optimizing performance and cost efficiency.
When faced with equipment failure, organizations often must decide between replacement and repair. This decision is influenced by factors such as the age of the equipment, the cost of repair, and the potential for improved technology. A thorough assessment of these factors is essential to make informed decisions that align with operational goals and budgets.
Monitoring systems that utilize data analytics play a significant role in enhancing the reliability of Industrial Electronic Equipment. By continuously tracking performance metrics, organizations can identify trends and anomalies that may indicate emerging issues. This proactive approach to monitoring helps minimize disruptions and improve overall equipment efficiency.
Future Trends in Industrial Electronic Equipment
The integration of IoT in industry is revolutionizing the landscape of Industrial Electronic Equipment. IoT devices enable real-time monitoring and data exchange, facilitating more informed decision-making. By connecting various equipment and systems, organizations gain insights that enhance operational efficiency and enable predictive maintenance strategies.
Advancements in AI and machine learning are transforming the capabilities of Industrial Electronic Equipment. These technologies enable data-driven decision-making, allowing for improved process optimization and automation. AI algorithms can analyze large volumes of data from equipment to identify patterns and make recommendations that enhance performance and productivity.
Energy-efficiency improvements are a significant focus for Industrial Electronic Equipment manufacturers. With rising energy costs and environmental concerns, companies are increasingly seeking solutions that reduce energy consumption while maintaining performance. Innovations such as variable frequency drives and energy-efficient motors contribute to more sustainable industrial operations.
Smart manufacturing solutions are emerging as an essential component of Industrial Electronic Equipment, integrating advanced technologies such as AI, IoT, and big data analytics. These solutions enable organizations to achieve higher levels of automation, customization, and responsiveness to market demands, ultimately driving competitive advantage.
Cybersecurity in industrial systems is becoming increasingly important as industries incorporate more digital solutions. Industrial Electronic Equipment is often targets for cyber-attacks, leading to potential disruptions. Therefore, manufacturers must prioritize robust cybersecurity measures to protect their systems and data from malicious threats.
Choosing Industrial Electronic Equipment Suppliers
When selecting suppliers for Industrial Electronic Equipment, assessing quality and reliability is paramount. Organizations should consider suppliers with a proven track record of delivering high-quality products that meet industry standards, as this directly impacts operational performance and safety.
Understanding pricing structures is crucial when evaluating potential suppliers of Industrial Electronic Equipment. Organizations must weigh the costs against features, support, and warranty options to ensure they receive the best value for their investment. Transparent pricing helps prevent unexpected expenses down the line.
Supplier certification and standards play an important role in selecting reliable partners for Industrial Electronic Equipment. Organizations should prioritize suppliers who adhere to recognized industry certifications and standards, ensuring that products comply with safety and quality requirements.
Evaluating customer support services offered by suppliers is essential for maintaining Industrial Electronic Equipment. Responsive and knowledgeable support can significantly reduce downtime and improve troubleshooting efforts, contributing to overall operational efficiency.
Comparing warranty and service agreements is a vital consideration when choosing suppliers for Industrial Electronic Equipment. Organizations should look for comprehensive warranties that cover repairs and replacements, as well as service agreements that provide ongoing maintenance and support to prolong the lifespan of their equipment.